As we’ve had some sunny days here in the UK recently, I’ve begun to think about projects for warmer weather and the fibres that are suitable for them.
One of my favourites is linen – strong, light and cool, with a subtle sheen and an amazing propensity for creasing. Linen yarn tends to polarise those who have tried it, as – unlike wool – it has no stretch, give or bounce. I’ve found when knitting that this means I have to make adjustments to my tension to avoid unduly strain on my hands and unpleasantly tight stitches.
Once you get used to it, however, it creates a delightfully breathable fabric with body and drape that’s perfect for sun and high humidity.
Last summer I visited a flax grower in the Cotswolds to see how these plants are grown and worked to become linen yarn. Now, a mere eight months later, I thought I’d share my photos and a description of the wonderfully named processes involved.
A trip to the Cotswolds
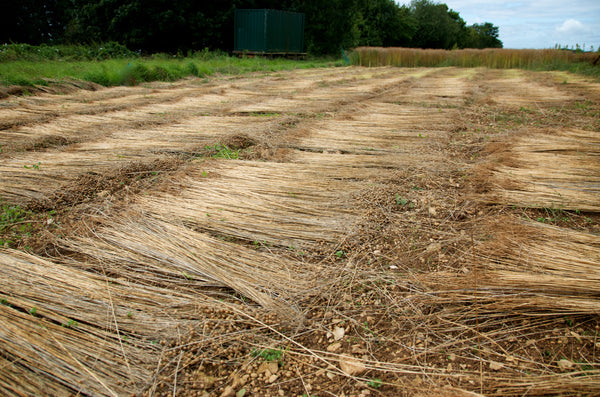
Retting and drying in the field
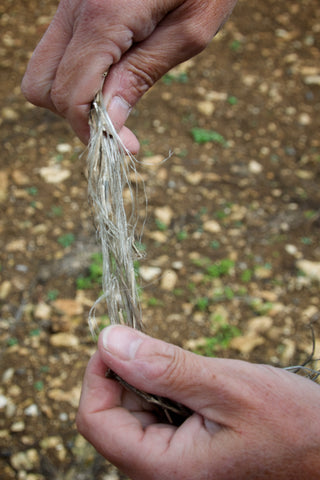
It’s easy to check when the retting is complete. Grasping a single stalk with a few centimetres between each hand, and pushing the hands together, scrubbing and crushing the stem, then pulling apart, should break off the outer bark leaving the inner fibres intact.
Insufficient retting means the bark clings on and won’t break away – the stems can then be left to ret a little longer. Too long exposure to moisture leaves a blackened, rotten stem that snaps easily and is smelly and useless.
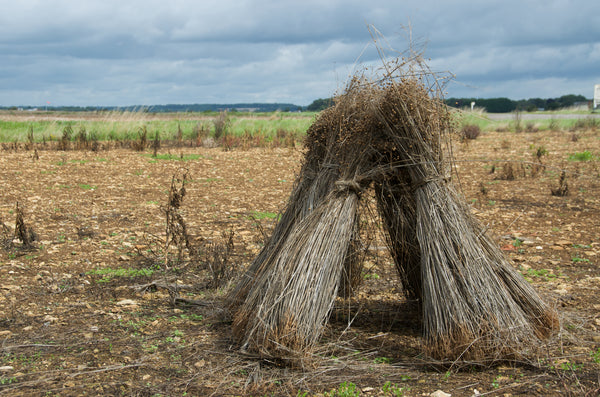
Breaking, scutching and hackling
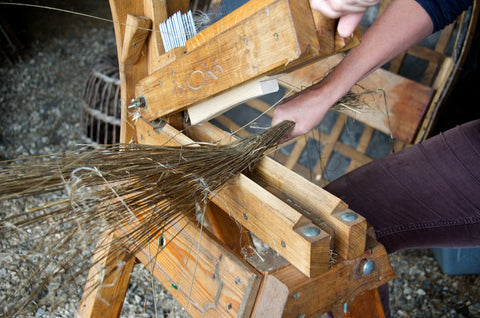
Done fast and repeatedly, this bends the flax in a specific area and causes the brittle outer bark to crack and begin to flake off. The flax is moved so that different sections are between the blocks.
Once the entire length has been ‘broken’, scutching removes the majority of the broken fragments of bark from the useful fibres. One end of the flax bundle is grasped firmly, and a long paddle with a tapered edge held in the other hand sweeps briskly down the length of the fibres. The bundle is frequently turned and rotated to ensure all areas are thoroughly scutched.
At this stage the flax looks a lot more like a useable fibre, but a lot of the individual strands are still a little stuck together. Hackling separates out the staples into the finest, softest lengths of fibre and helps pull out any shorter and weaker fibres (called ‘tow’).
Again the handful of flax is grasped tightly, and pulled through a literal bed of nails – the hackle – at speed to comb it out. Ever wondered why a dog's hackles are named so? This is why!
The flax is drawn through sets of progressively finer hackles, resulting eventually in a beautifully soft, glossy bundle of long, grey-beige fibres.
Spinning flax fibre into linen yarn
The traditional solution is to prepare the fibre on a distaff – a cone-shaped device that holds the flax and prevents it from tangling. We made a rudimentary distaff from card, stuffed with newspaper and mounted on a stick.
The flax is spread out in a fan shape, then the pointed end of the distaff is placed at the base of the fan. The distaff is then rolled across the flax, which is gathered by hand onto the surface of the distaff, coating it in layers.
The distaff is then turned upright and the flax gently tied on with ribbon to hold it in place. For spinning, the fibres can then be drawn from the base of the distaff, and it’s possible to spin incredibly finely, only twisting a couple of staples together.
I loved learning about this process and am so glad to have found somewhere quite near to me where I can source locally grown flax!
One of the things that did catch my eye as we worked was the flax tow – the fibre removed at the hackling stage.
Though these fibres are a 'second-rate’ waste product, I was sure that with time and care they could be used. I took home a large bag with me and have developed my own way of processing this to yield shorter staples that can be easily blended with other fibres. Maybe in another post I’ll write about this!
How about you? Have you worked with flax/linen in your craft work? I’d love to hear about how you’ve used it and your opinions in the comments below!